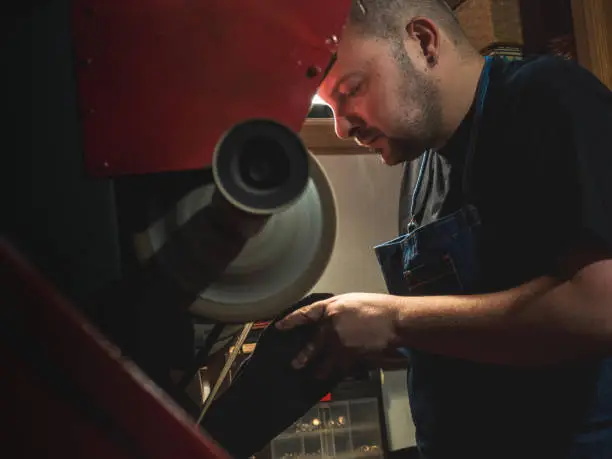
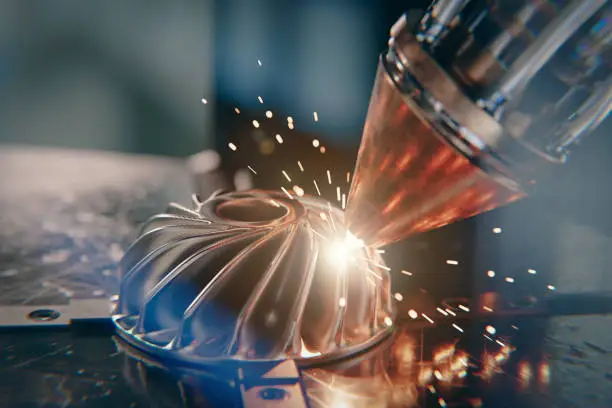
The Future of Metal Spinning with Advancing Technology
Despite being a centuries-old craft, metal spinning has evolved into a sophisticated and highly versatile manufacturing process that today holds a crucial place in various industries. From its origins in hand-crafted methods to the development of advanced CNC machines, metal spinning has continually adapted to technological advancements.
Modern metal spinning offers an unmatched solution for businesses and manufacturers looking to create precise, complex shapes with a high degree of repeatability.
In this article, we will explore the future of metal spinning and how advancing technology is shaping the industry, particularly in the UK, where metal spinners are leading the charge in innovation and capability.
A Brief Overview of Metal Spinning
At its core, metal spinning involves placing a metal disc onto a rotating lathe while applying pressure to meld the metal into a specific shape. This technique allows for the creation of symmetrical, cylindrical, or conical forms without the need for additional tooling. Metal spinners have used this process for centuries, traditionally by hand. Today, modern advancements such as CNC (Computer Numerical Control) machines have automated much of the process, making it faster, more accurate, and more efficient.
For industries such as aerospace, automotive, and lighting, where precision and strength are paramount, metal spinning offers an ideal solution. In the UK, companies like Tanfield Metal Spinners are at the forefront of this technology, producing a wide range of spun metal parts using state-of-the-art equipment.
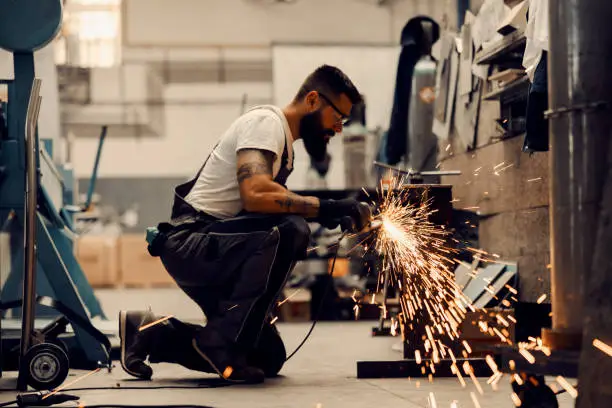
Technological Advancements in Metal Spinning
Technology is transforming the landscape of metal spinning in several ways, particularly through automation and precision. As businesses demand more intricate designs with tighter tolerances, CNC metal spinning machines are becoming indispensable. These machines can store and repeat exact settings, ensuring consistency and high-quality production runs. For example, the introduction of CNC programming means spinners can automate processes that were once labour-intensive, reducing the time required to produce complex components.
One of the significant technological advancements in metal spinning is the development of machines capable of handling larger and thicker materials. For example, the PNC 1200 machine allows metal spinners to produce parts up to 2500mm in diameter and 15mm in thickness for mild steel. This capability opens new doors for industries requiring larger, more durable components.

Benefits of Automation and CNC Metal Spinning
Automation has brought several key advantages to metal spinning. Firstly, it significantly reduces the need for manual intervention, allowing for greater consistency in production. With CNC metal spinning, settings can be adjusted and saved, enabling spinners to produce complex shapes with pinpoint accuracy. This is particularly beneficial when producing parts that must adhere to strict tolerances.
Additionally, the automation of the spinning process has increased efficiency. CNC machines can operate at much higher speeds than manual spinners, drastically reducing production times. According to industry reports, these machines can be up to 15 times quicker than manual processes, resulting in faster turnaround times for clients.
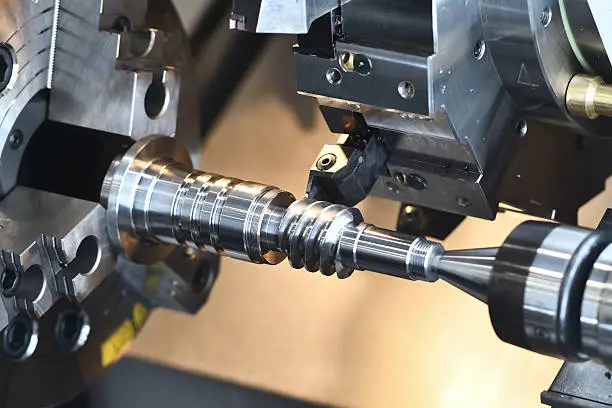
Material Innovation in Metal Spinning
The materials used in metal spinning have also evolved with technology. While traditional materials such as mild steel and aluminium remain popular, advancements in metallurgy have introduced new options that offer superior strength, durability, and corrosion resistance. These materials include high-strength alloys that can withstand the pressures of spinning without deforming, making them ideal for critical applications such as aerospace components and pressure vessels.
Modern CNC machines can handle a wide range of materials, from soft metals like aluminium to harder ones like stainless steel. The ability to work with tougher metals has expanded the potential applications of metal spinning, particularly in industries where performance under extreme conditions is essential.
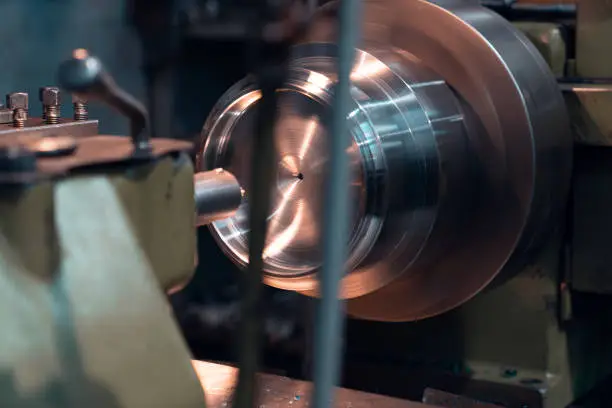
The Importance of Prototype Development
As metal spinning technology advances, the importance of prototype development cannot be overstated. Creating a prototype allows manufacturers to test a component’s design, functionality, and performance before committing to full-scale production. This iterative process ensures potential issues are identified and resolved early, reducing the risk of costly errors downstream during production.
Prototypes are particularly valuable in industries that demand high precision, such as aerospace and medical devices. By subjecting a prototype to rigorous testing, manufacturers can verify that it meets all necessary specifications and performs as expected under real-world conditions. This process also allows for adjustments in material selection, tolerances, and design, ensuring the final product is optimised for performance and cost.
The Future of Metal Spinning
Metal spinning looks set to take even greater technological strides in the near future with the integration of advanced technologies such as artificial intelligence (AI) and machine learning (ML). These technologies have the potential to take CNC metal spinning to new heights by further optimising production processes and predicting potential issues before they arise. AI can analyse vast amounts of data from spinning operations, enabling manufacturers to fine-tune their processes for even greater efficiency and reduced waste.
Another promising area of development is the use of simulation software to model spinning operations before they are performed. Manufacturers can identify potential issues with material flow, stress points, and deformation patterns by simulating the spinning process. Such simulation essentially creates virtual prototypes, allowing adjustments to be made in the design phase, further improving the quality of the final product.
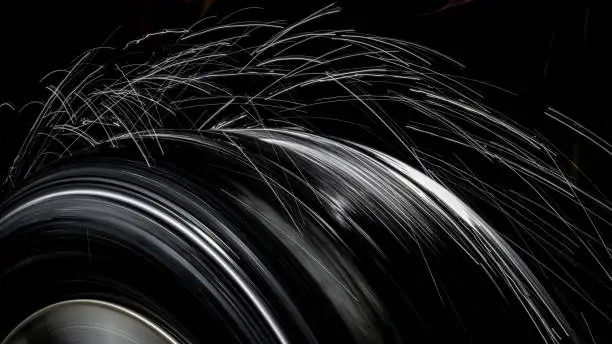
Finally, advancements in additive manufacturing techniques, such as 3D printing, are also beginning to influence metal spinning. Hybrid machines that combine spinning with 3D printing capabilities could revolutionise the industry by enabling the manufacture of complex geometries that would be difficult or impossible to achieve with traditional spinning techniques.
The Future is Spinning
Metal spinning may be an age-old technique, but it continues to evolve with the times thanks to advancing technology. The introduction of CNC machines, automation, and material innovation has already transformed the industry, allowing for greater precision, faster production times, and the ability to handle more complex projects. As technology continues to develop, the future of metal spinning looks even brighter, with further opportunities for increased efficiency, cost savings, and creative design possibilities.
The future promises enhanced capabilities and innovations for businesses needing high-quality spun metal products. With companies like Tanfield Metal Spinners leading the way in the UK, the metal-spinning industry will continue to meet the demands of an ever-evolving manufacturing landscape.
If you’re interested in learning more about how metal spinning can help your business or need a quote for your next project, contact our specialists today.
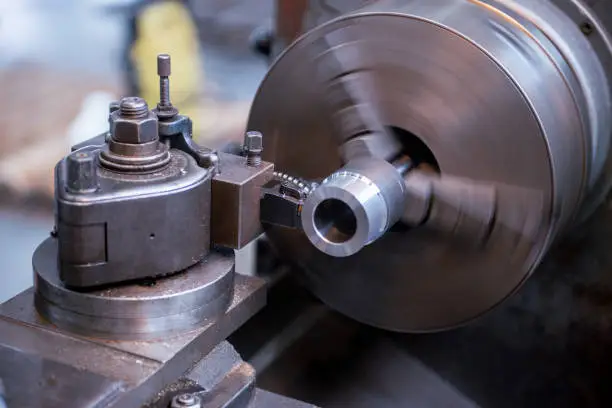